Auburn
Well-known member
Update: After some re-design work (thanks to Snowman for the ideas). As it sits, the whole thing weighs in at 170 lbs. I have about 15 pounds of side and lid panels to add. That will bring it in 120 lbs lighter than the first version and 20 lbs heavier than the bushtec. Right in my target area. Here are pictures of where I am at so far.You got me re-thinking a few things to help lighten it up.You could possibly save more weight by lowering your longitudinal runners on the sides down and using them to cap the lateral supports. Right now you have a framework on top of a frame; try to combine them into one piece.
The outside trailer dimensions are 26" wide at the front, widens out to 41" at the wheels, then goes back into 25" at the rear. The space inside from the cooler back is 14" x 24" which will allow me to carry a spare front wheel, rear wheel and trailer wheel (all with tires mounted) standing vertically for the. The space in front of the cooler is 30" deep 25" at the front x 41" at the rear. Overall inside height is 26". The cooler is 14" x 24". The plywood on the bottom and sides is 3mm baltic birch and is 3 ply, very lite and very strong. The fenders over the wheels is 20 gage steel.
The trailing arms could be lighter, but I erred on the side of strength by using 3/8" x 1.5" flat bar stock instead of tubing. I could save another 5-7 lbs here if I switched to tubing. I also made them about 1 foot longer than before to give them a better angle to work within.
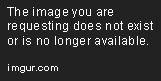
Top view with the lid up (lid weighs 12 lbs). The bare frame without the wood, tires, lid, or shocks weighed 75 lbs.
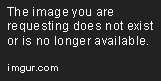
Here is a shot with the ice chest in place. The wood box under the cooler is for my tools to keep them all in one place. I also have a pocket built into it that carries a Yusua battery for the FJR and use it to power the cargo light when the lid is up. It gets charged by the bike going down the road.
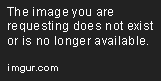
Over head shot of the main cargo area with cooler out.
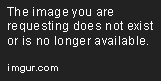
Cooler in
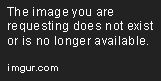
Last edited by a moderator: